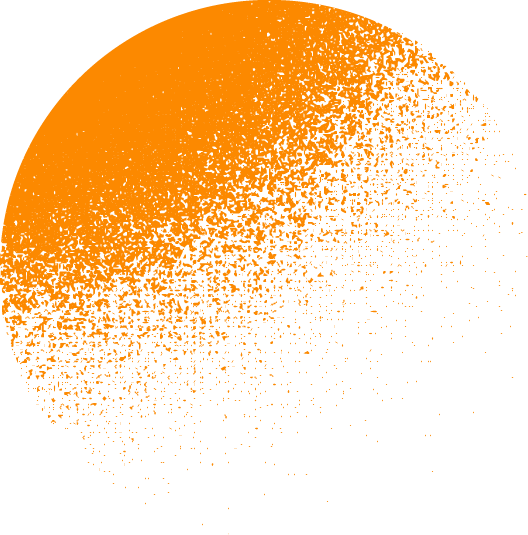
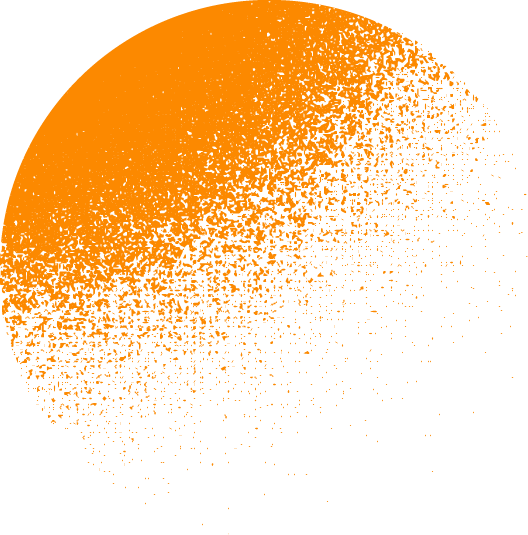
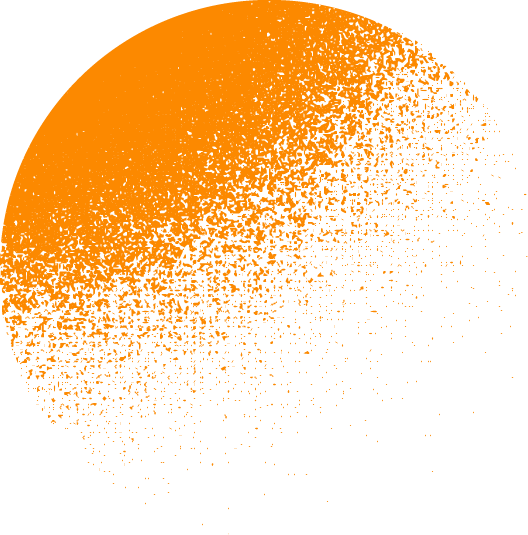
Lean Six Sigma Green Belt
BUSA-41006
Click Here to Watch Our Free Info Session Anytime!
Improve Performance, Enhance Quality, Reduce Costs
Lean Six Sigma (LSS) is a proven methodology for improving business performance by reducing variation and optimizing processes. Green Belts play a key role in leading process improvement efforts, solving business challenges, and driving operational excellence.
Through real-world applications, you’ll learn how to identify improvement opportunities, collect and analyze data, and implement meaningful changes. Whether you're looking to advance in your career or make a measurable impact in your organization, this course will give you the foundation to lead process improvement efforts with confidence.
Program Benefits
-
Apply the established LSS principles to a real-life project.
-
Receive guided coaching and mentorship from a Master Black Belt, and know how to best apply the proven techniques and strategies.
-
Earn PDU's and submit to the Project Management Institute (PMI); maintain your PMP certification.
-
Graduates receive a verifiable digital credential and are prepared to progress into LSS Black Belt.
Who Should Attend?
Any team or individual responsible for managing or participating significantly in any business process activities including managers, professionals, and line staff. Any process. Any industry.
Project-Based Training
As a Green Belt student, you have several options: bring a process improvement project from your workplace, collaborate on a group project with fellow students, partner with a local nonprofit, or gain hands-on experience by offering internship-style support to an organization of your choice.
Unless students work together, group projects are only permitted in the Live Online or In-Class formats.
Prove you can deliver real results.Studies show that people retain up to 90% of what they learn by applying it—compared to just 10% through reading alone. Completing a real-world project not only reinforces your skills but also delivers measurable impact. On average, projects save at least $40,000 annually—showcasing your ability to drive real change.
Watch: The Power of LSS Class Projects (3 minutes)
e FAQs below.
What are Graduates Saying?
-
"I really appreciated the instructor's professional experience in the content of the course. Their knowledge really came through. Both are great instructors as well, how they interact with students, give meaningful feedback, and structure the course."
-
"I liked that this class involves actually improving a process! It made implementing a lean six sigma project a lot easier since we could ask the instructor questions over the span of the project!"
-
"I liked that the Instructor was with us every step of the way. It seemed daunting at the beginning what we were to achieve, but with her guidance it became easier and easier."
-
"I enjoyed this course very much and the materials provided were excellent. Easy to follow and implement."
In a recent Alumni Survey, 95% of graduates confirmed that UC San Diego's Lean Six Sigma training has helped them improve their work performance and/or the efficiency of their team.
No Interest Payment Plan
Our no-interest payment plan divides tuition into manageable monthly payments. An initial payment is required for registration processing, with subsequent payments due on the 15th of each month. Click here to request a: No-Interest Payment Plan.
Click HERE to watch a Lean Six Sigma Information Workshop
|
Questions?
We’re here to help! Our team is dedicated to ensuring you have all the information you need to make an informed decision about your education.Contact Your Program Manager, Angela Miller
📅 Schedule a Phone Appointment or email: ProcessPrograms@ucsd.edu
Course Information
Course sessions
Section ID:
Class type:
This course is entirely web-based and to be completed asynchronously between the published course start and end dates. Synchronous attendance is NOT required.
You will have access to your online course on the published start date OR 1 business day after your enrollment is confirmed if you enroll on or after the published start date.
Textbooks:
No textbook required.
Policies:
- No refunds after: 8/3/2025
Note:
Schedule:
Instructor:
Sabine Rentschar

Starting her 20+ year long career in the Automotive Industry in Germany, Sabine was exposed to and worked with Lean Manufacturing and Six Sigma Principles from the very beginning. She has worked for a small start-up in High Performance Drive Technologies and Control Systems as well as in large corporations in the Optical Industry being responsible for Operations Technology, Development, Application and Optimization of Processes and Equipment. She was part owner of an Optical Wholesale Manufacturing Lab and has led and managed many teams and businesses. Throughout her career Sabine has successfully implemented numerous Continuous Improvement and Quality Programs and Projects with a constant focus on Process and Performance Improvement.
An Industrial Mechanic by trade with a Masters of Engineering in Mechatronics / Systems Engineering, Sabine is also a certified Lean Six Sigma Black Belt, a certified PMP and is an active board member of her local ASQ Section in Southern California and two other not-for-profit organizations.
Section ID:
Class type:
Textbooks:
No textbook required.
Policies:
- No refunds after: 8/28/2025
Note:
Schedule:
Date | Day | Start | End |
---|---|---|---|
8/22/2025 | Fri | 9:00 a.m. | 12:00 p.m. |
8/29/2025 | Fri | 9:00 a.m. | 12:00 p.m. |
9/5/2025 | Fri | 9:00 a.m. | 12:00 p.m. |
9/12/2025 | Fri | 9:00 a.m. | 12:00 p.m. |
9/19/2025 | Fri | 9:00 a.m. | 12:00 p.m. |
9/26/2025 | Fri | 9:00 a.m. | 12:00 p.m. |
12/5/2025 | Fri | 9:00 a.m. | 12:00 p.m. |
Section ID:
Class type:
This course is entirely web-based and to be completed asynchronously between the published course start and end dates. Synchronous attendance is NOT required.
You will have access to your online course on the published start date OR 1 business day after your enrollment is confirmed if you enroll on or after the published start date.
Textbooks:
All course materials are included unless otherwise stated.
Policies:
- No refunds after: 10/5/2025
Note:
Schedule:
Instructor:
Sabine Rentschar

Starting her 20+ year long career in the Automotive Industry in Germany, Sabine was exposed to and worked with Lean Manufacturing and Six Sigma Principles from the very beginning. She has worked for a small start-up in High Performance Drive Technologies and Control Systems as well as in large corporations in the Optical Industry being responsible for Operations Technology, Development, Application and Optimization of Processes and Equipment. She was part owner of an Optical Wholesale Manufacturing Lab and has led and managed many teams and businesses. Throughout her career Sabine has successfully implemented numerous Continuous Improvement and Quality Programs and Projects with a constant focus on Process and Performance Improvement.
An Industrial Mechanic by trade with a Masters of Engineering in Mechatronics / Systems Engineering, Sabine is also a certified Lean Six Sigma Black Belt, a certified PMP and is an active board member of her local ASQ Section in Southern California and two other not-for-profit organizations.
Section ID:
Class type:
All class meetings held in-person according to published location, dates and times. Students may be expected to engage with course content online during the published course dates.
Textbooks:
No textbook required.
Policies:
- No refunds after: 10/8/2025
- 1st no meeting date: 10/9/2025
Note:
Schedule:
Date | Day | Start | End | Location |
---|---|---|---|---|
10/2/2025 | Thu | 9:00 a.m. | 3:00 p.m. | Room 115, UCSD Division of Extended Studies University City Center, 6256 Greenwich Drive, San Diego |
10/16/2025 | Thu | 9:00 a.m. | 3:00 p.m. | Room 115, UCSD Division of Extended Studies University City Center, 6256 Greenwich Drive, San Diego |
10/23/2025 | Thu | 9:00 a.m. | 3:00 p.m. | Room 115, UCSD Division of Extended Studies University City Center, 6256 Greenwich Drive, San Diego |
10/30/2025 | Thu | 9:00 a.m. | 3:00 p.m. | Room 115, UCSD Division of Extended Studies University City Center, 6256 Greenwich Drive, San Diego |
11/6/2025 | Thu | 9:00 a.m. | 3:00 p.m. | Room 115, UCSD Division of Extended Studies University City Center, 6256 Greenwich Drive, San Diego |
1/15/2026 | Thu | 9:00 a.m. | 3:00 p.m. | Room 115, UCSD Division of Extended Studies University City Center, 6256 Greenwich Drive, San Diego |
Instructor:
Tracy Orourke Salguero, MBA, MBB

Managing Partner, Integris Performance Advisors
Tracy is the Co-Founder of the Just-in-Time Cafe and a co-author of the book, "The Problem-Solver's Toolkit: A Surprisingly Simple Guide to Your Lean Six Sigma Journey". By sharing over 20 years of expertise, she makes it easier for people to learn and apply Lean Six Sigma to achieve their goals.
She loves spearheading the implementation of Lean Six Sigma by providing training, consulting and coaching on many aspects of cultural change, including leadership development, customer experience, strategic alignment and process improvement.
Why She Loves Teaching
"I love the "A-Ha!" moment when someone realizes that this stuff (Lean Six Sigma) works. It's obvious that they now see differently a fresh perspective – on a whole new world around them. This is why Proust's quote (below) resonates with me. Witnessing the moments of seeing with new eyes energizes me and drives me to do what I do."
Professional Summary
Tracy got her start as a Six Sigma Black Belt at GE Appliances in the late 1990s with Jack Welch at the helm. After a Black Belt career at GE, she became a Lean Six Sigma Consultant and has helped many organizations with all aspects of Lean Six Sigma.
She is an accomplished facilitator, trainer, coach and presenter. She has trained over 2,000 people, mentored 500+ people and has helped complete 400+ projects with results that range between $50,000 and $8 million dollars in savings.
Her facilitation expertise runs the gamut, from facilitating leadership retreats with executives to coaching managers on Leader Standard Work, and facilitating Process Walks and Kaizen Events with front line employees and project teams.
Credentials
MBA with emphasis in Leadership and Managing Organizational Change from the Graziadio School of Business at Pepperdine University
Certified Black Belt – GE Appliances
Certified Master Black Belt Certification – Pivotal Resources
Lean Enterprise Institute (LEI) Workshop – Leader Standard Work, Visual Management
Five Behaviors of a Cohesive Team - Accredited Facilitator
Certified Green Belt Instructor – Motorola University
The Leadership Challenge (TLC) – Accredited Facilitator
Lean Enterprise Certificate – San Diego State University
BA in English Literature from San Francisco State University
Section ID:
Class type:
Textbooks:
No textbook required.
Policies:
- No refunds after: 10/16/2025
Note:
Schedule:
Date | Day | Start | End |
---|---|---|---|
10/10/2025 | Fri | 9:00 a.m. | 12:00 p.m. |
10/17/2025 | Fri | 9:00 a.m. | 12:00 p.m. |
10/24/2025 | Fri | 9:00 a.m. | 12:00 p.m. |
10/31/2025 | Fri | 9:00 a.m. | 12:00 p.m. |
11/14/2025 | Fri | 9:00 a.m. | 12:00 p.m. |
11/21/2025 | Fri | 9:00 a.m. | 12:00 p.m. |
1/8/2026 | Thu | 9:00 a.m. | 12:00 p.m. |
Instructor:
Sabine Rentschar

Starting her 20+ year long career in the Automotive Industry in Germany, Sabine was exposed to and worked with Lean Manufacturing and Six Sigma Principles from the very beginning. She has worked for a small start-up in High Performance Drive Technologies and Control Systems as well as in large corporations in the Optical Industry being responsible for Operations Technology, Development, Application and Optimization of Processes and Equipment. She was part owner of an Optical Wholesale Manufacturing Lab and has led and managed many teams and businesses. Throughout her career Sabine has successfully implemented numerous Continuous Improvement and Quality Programs and Projects with a constant focus on Process and Performance Improvement.
An Industrial Mechanic by trade with a Masters of Engineering in Mechatronics / Systems Engineering, Sabine is also a certified Lean Six Sigma Black Belt, a certified PMP and is an active board member of her local ASQ Section in Southern California and two other not-for-profit organizations.
FAQs
UC San Diego also embraces a Lean Six Sigma culture. To date, over 6,000 staff members have pursued process improvement training. This has empowered and enabled us to identify, assess, and solve issues with a customer-centric balance of efficiency and effectiveness. We invite you to join the community, and apply process improvement at your organization!
Click here to watch a short video: UCSD’s Lean Journey.
- A trusted name in Lean Six Sigma, with robust certificate programs for 25+ years.
- World Class Instructors: Trainings are conducted by a team of skilled LSS Master Black Belts and Lean experts, including Tracy O’Rourke, Jim Athon, Sabine Rentschar, Brion Hurley, Luis Socconini, Phaniendra Somraj, Pete Thurman, Elisabeth Swan, and Mike Osterling.
- Small Classrooms: Classes are limited to 16 - 22 students, to allow for ample coaching and project mentorship. As such, space is limited and registering early is recommended.
- Project Application: We exemplify the model of Learn By Doing. To earn a Green and Black Belt, all students must improve a real business process as part of the training.
- Project Coaching and Mentorship: Students have the opportunity to apply the Lean Six Sigma tools and concepts under the guidance of an experienced Master Black Belt. All trainings are comprehensivec, collaborative, and instructor led.
- Earn a verifiable digital credential, which can be shared on social media, and with colleagues and employers to recognize your achievement.
- Trusted by some of San Diego’s leading organizations, including Dexcom, SHARP, Costco, Illumina, UCSD Health, to name a few. We also focus on training fellow educational institutions, including a variety of University of California campus’ and University’s across the country.
Students can also view their final grades and download an official transcript through their MyExtension student portal.
Those who complete both the Green and Black Belt programs will receive a specialized certificate, mailed directly to them.
- Measurable: Either the data needed for the project already exists or may be readily gathered. That is, there is a clearly identifiable unit, and you can quantify what makes that unit defective
- Existing Process: DMAIC assumes an existing process that has one or more deficiencies or inefficiencies that need to be addressed. It is not optimal for new process development.
- Incremental Improvement: DMAIC is designed to diagnose and address only one (or a few) issues at one time and is not intended for wholesale re-design of a process.
- Financial Results: You can clearly demonstrate the financial (or other genuine business) benefits of improving the process.
- Unknown Root Cause: If you are sure you know what is causing the variation in your process, fix it! DMAIC assumes we don’t know exactly where the process is broken, or why.
- Unknown Solution: If we know what to do to fix the problem, and it is cost-beneficial, fix it! DMAIC assumes we don’t yet know how to fix it, especially since we don’t know where it is broken!
The more advanced Black Belt project accounts for 53% over the final grade. The Black Belt Project must show projected cost savings of at least $100,000 annualized hard savings. The final project presentation must Show use of Tools, Actions taken to modify a process, quantifiable Results, and Controls to assure process sustains improvement. The presentation must include the application of Lean Six Sigma tools and concepts, and include the following:
- Project Charter
- SIPOC
- Process Map (basic, swim lane, VSM, etc. as appropriate)
- 5 Why’s matrix
- Other tools as appropriate to your project type
- Hypothesis testing using SPC XL to determine root cause(s)
- Hypothesis test to verify quantifiable results on Primary Metric
- Primary Metric that demonstrates improvement
- Control Plan
- HUMAN RESOURCES: Improve and simplify the employee onboarding process. Students saved 2,000 hours/year and reduced email handling by 60%.
- MANUFACTURING: 60% reduction in remakes and reworks, saving $150k a year.
- BIOTECH: 50% reduction in leakage of bioreactor product, resulting in $80k saved each year.
- EDUCATION: Reduced the training preparation time by 72%, from 7 to 2 hours.
- EVENT PLANNING: Streamlined the event registration process, and reduced activity planning lead time by 81% (38 steps to 7).
- FINANCE: Reduced the time to prepare quarterly reports by 72%, from 16 - 4.5 days.
- SUPPLY MANAGEMENT: Reduced warehouse transportation time, resulting in an annal savings of $60k.
You should consider a “problem” with the process (errors, customer complaints, delays, etc.). Don’t focus on how you are going to fix the problem because the intent to learn the Lean Six Sigma methodologies and apply the tools to identify and continuously improve your process.
We find that the best kind of project (or process) to select is something that is a measurable problem that needs to be solved and can be broken down (or walked through) and analyzed. For example, reducing defects or improving speed. A project that focuses on communication, for example, can be a challenge as it’s hard to determine whether the communication is better.
Consider how you would measure the before and after, and outcomes of improving a process.
By the end of the class, the project may not be completed, but there must be controls put in place so that you can evaluate the projected annual savings.
Classes are limited to 16 - 20 students, to allow for ample coaching and project mentorship. As such, space is limited and registering early is recommended.
Note that the Black Belt level project is much larger in scope, and students must achieve a cost savings of $100k, projected annually.
- Join the Business Excellence Community
Connect with UC San Diego faculty and staff who are committed to continuous improvement. Explore a variety of free events—including webinars, conferences, and networking sessions—designed to help you sharpen your skills, share best practices, and expand your network. Learn More. - Attend Process Palooza
Be part of UC San Diego’s annual celebration of continuous improvement! Process Palooza is a high-energy, interactive event where you can engage with others at every stage of their Lean Six Sigma journey—whether you're just starting or looking to grow your impact. https://processpalooza.ucsd.edu/ - Join the LSS Alumni Mixer
Lean Six Sigma graduates are invited to an annual in-person alumni mixer—a great way to reconnect, share experiences, and continue learning. To receive updates about the next event, contact processprograms@ucsd.edu. - Connect on LinkedIn
Join our Lean Six Sigma Alumni LinkedIn group, home to a growing network of over 600 professionals. Stay in touch with fellow grads, hear about job opportunities, and share your continuous improvement wins.
In Pathway 2, students complete the Lean Six Sigma Green Belt and Lean Six Sigma Black Belt separately in two courses.
- Live Online - interactive, instructor-led, and real-time. Class sessions take place LIVE via Zoom, simulating the in-person experience.
- Asynchronous Online – login and complete class work anytime 24/7. All courses use Canvas, an online learning management system that allows you to complete assignments, share documents, and take tests and quizzes remotely. You will also have the option to schedule LIVE individual or group project coaching sessions with the instructor, hosted via Zoom.
- How many times each month/year is the process used?
- How long the process takes each time it is used?
- What defects/errors arise along the way and how often do these occur?
- What are the material costs involved in the process?
- What are the impacts if we do not find a better way to move through this process?
- Are there any glaring areas of waste or rework?
Please note that you’ll need to manually enter the course details rather than select from the pre-populated drop down menus. If you click on the ? mark symbol by each field it explains this. This will allow you to enter the provider name, course title, etc.
- Staff and faculty discounts
- Programs for the unemployed or underemployed
- Private student loans
- And more…
If you are a veteran who served in our armed forces, you may be eligible to use your veteran education benefits to cover some or all of your program tuition. Please review our Veterans Education Benefits page for details. You are also welcome to reach out to the Extended Studies Veteran’s team by contacting unex-veterans@ucsd.edu.
Additional Discount or Scholarship Opportunities:
- San Diego Project Management Institute (PMI-SD) chapter members may be eligible to receive discounts on LSS courses. Click here for details.
- UCSD Lean Six Sigma Staff Scholarship - Visit OSI.UCSD.EDU for details.
- UCSD Health staff may be eligible to pursue Lean Healthcare Training, which is provided at no cost.
- Focus on "customer": Identify your customers, whether that is clients, vendors, patrons, other departments, etc. Once you have your customers identified, gather their input on their goals and pain points. As your project moves forward, involve your customers in the discussions, along with your Subject Matter Experts.
- Don't jump to improve: Strive to address a root cause. Leverage data to validate ideas, and pilot changes to check for downstream considerations. This will drive you towards averting fires, rather than frantically extinguishing them.
- Empower staff at all levels: Process knowledge and ideas should be generated from the staff who perform the work. The Lean Practitioner facilitates discussions and manages the project, but the teams provide and implement solutions. Not only does this secure creative and effective ideas, but it also facilitates change management and longevity of your outcomes.
- Explore assumptions and ask ‘Why’: Dig deeper to clear obstacles we have created for ourselves over time. For example, if you hear "There's a policy which drives that step," then consider whether the policy has changed, or whether other comparable departments have interpreted and implemented the policy differently. If you hear "We've always done it that way" then prompt your team to consider whether it has to be done that way.
While the training material is software-neutral, students are welcome to utilize their organization's desired software.
If requested, we can also provide training materials specific to Minitab.
Statistical tools are not provided for the Green Belt level.
If you are a veteran who served in our armed forces, you may be eligible to use your veteran education benefits to cover some or all of your program tuition. Please review our Veterans Education Benefits page for details.
Are you a member of the San Diego Chapter of the Project Management Institute? If so, you are eligible for a 20% tuition discount on select Project Management courses. To request your discount, please complete this required request form at https://forms.gle/CEAjJFENq6NNZja37
If you are paying for a course with a purchase order, you must submit your purchase order on company letterhead:
- By email to unex-cashiering@ucsd.edu
- By fax: (858) 822-2243, attn: Financial & Business Services
- By mail to: UC San Diego Division of Extended Studies, attn: Financial & Business Services, 9500 Gilman Drive, MC 0170F, La Jolla, CA 92093-0170.
Payment is due upon receipt of your invoice. We require the following information on all purchase orders:
- Company’s complete name and address
- Purchase order number
- Invoicing address and telephone number
- Point of contact (name, email, and telephone number)
- Student’s name, email, telephone number and mailing address
- Section ID number, course title, course dates and course fee amount
- Authorizing signature(s)
If you have any questions about purchase orders, please call us at (858) 534-3117.