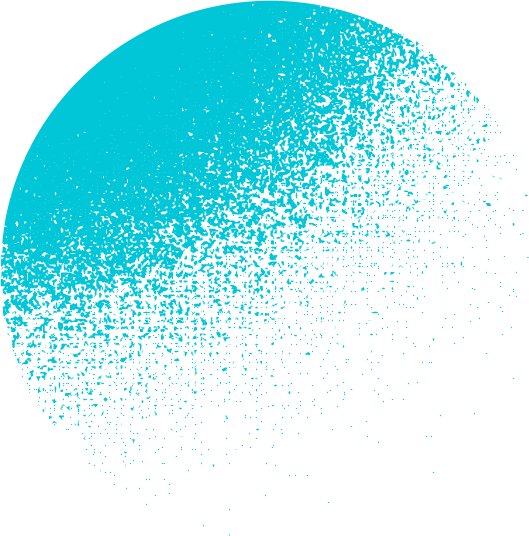
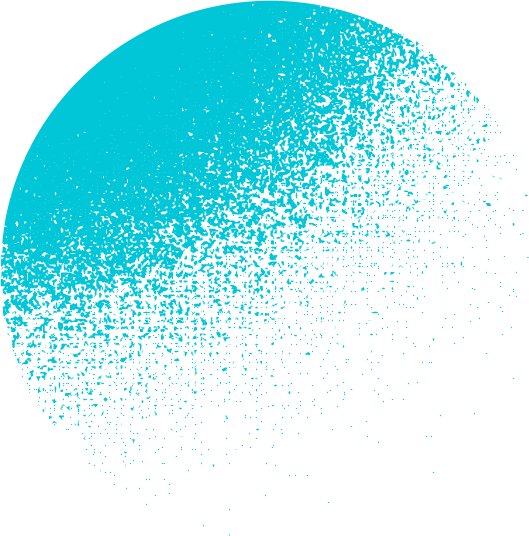
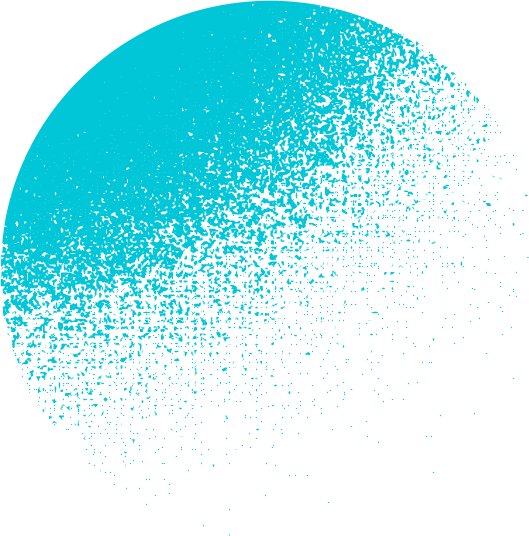
11 February 2023
How to Build a Corporate Culture Centered Around Process Improvement

Process improvement strategies—business methodologies for efficiency and effectiveness—can have a tremendous impact on an organization. They can reduce costs, speed up production time, facilitate innovation, satisfy customer needs and foster an environment where employees feel like they have a stake in improving the final product.
The challenge of process improvement is that it’s not easy. It takes constant review and monitoring, plus a willingness to change—and change often.
Luckily, there are defined methodologies for integrating process improvement into the culture of companies at every level. But that alone doesn’t make process improvement a given.
You may have studied all the tools and thoughtfully implemented the most well-respected methodologies of process improvement in your organization. Still, unless you have leadership and a corporate culture that embraces process improvement, it’s likely all your implementations will quickly revert to the old ways of doing business.
In this article, we’ll explore how to build a corporate culture centered around process improvement. We’ll explain one of the most popular process improvement methodologies, Lean Six Sigma, as well as some important points to consider as you build process improvement into the culture of your company.
The Lean Six Sigma Method of Process Improvement
What is Lean Six Sigma? It’s one of the most popular business methodologies for process improvement. It’s a fusion of two methodologies, Lean and Six Sigma, which are time-tested and widely regarded strategies that help organizations enhance processes, eliminate waste, streamline production, minimize errors and focus on delivering value to customers.
Lean is a process improvement toolkit that focuses on streamlining processes to deliver products and services in the most straightforward, efficient, and optimal way possible. Many of the improvements come from finding steps in the production process to shorten, eliminate, or combine. Making the most of inputs, such as materials and people power, are closely reviewed as well.
Six Sigma focuses on optimizing a process to create the highest quality outputs. There’s generally a special emphasis on minimizing errors, defects, and variability in the products the process creates. Developed by engineers at Motorola in the 1980s, it was originally intended for the manufacturing and assembly lines, where steps in a process can be easily isolated, examined and improved upon.
Combining Lean and Six Sigma
With their different points of emphasis, it doesn’t take a master of process improvement to see the value in combining the two. Together Lean Six Sigma provides a widely encompassing toolkit for solving problems, improving processes, working more efficiently and delivering value. While both processes were originally developed for manufacturing, they’ve since been adapted to everything from customer service, supply chain, healthcare and more.
When properly implemented, the methodology can lay the groundwork for a culture of process improvement within an organization. It asks practitioners to work on the process rather than in the process. Team members are constantly identifying potential areas of improvement and working to make changes based on a five-step process called DMAIC.
DMAIC stands for:
- Define: Clarifying the problem and part of the process to be improved.
- Measure: Choosing the key metrics and quantifying the baseline of current state.
- Analyze: Reviewing the process and the data to identify the most likely opportunities for improvement.
- Improve: Implementing the improvements and verifying their effectiveness.
- Control: Maintaining the updated process and continuing to refine it.
Creating a Process Improvement Culture in Your Workplace
The true power of Lean Six Sigma or process improvement in general is in the culture of continuous improvement that can spring out of it. If all goes well, the cultural shift can create an empowered, solutions-oriented workforce that is constantly improving the bottom line on their initiatives.
Employees become active participants in solving problems, rather than seeing something and leaving it for somebody else to deal with.
Yet it’s one thing to get your employees trained on Lean Six Sigma and bought into the strategy, but there’s also an important cultural shift that needs to happen to sustain it. Otherwise, employees might revert to the mindsets and behaviors that worked against process improvement in the first place.
Here are some points to consider to truly get process improvement to stick in a corporate culture.
Get Buy-in From Leadership
For process change to effectively stick as an aspect of corporate culture, it needs drive and support from leadership at the highest level. This includes everything from providing training to keeping time and space open for the process, to graciously rewarding team members in alignment with the process improvement goals.
Upper management teams that give lip service to change but remain stuck in old ways of doing things will find they are implicitly signaling to the rest of the company that they aren’t as on board with the idea as they say they are.
The process of change requires commitment and persistence. There’s significant upfront and continued investment that needs to happen. In the long run, this should pay incredible dividends, but if leadership is unsure of the value, they’ll undermine it too.
If the leadership isn’t committed and willing to embrace process improvement methodology for themselves, they can’t expect their employees to follow suit.
One method of engaging leadership is tackling a long-standing problem as a proof-of-concept project. Work with leadership to pick something meaningful yet manageable and pull a few Lean Six Sigma resources together to work on the project. This way the project will move faster, the likelihood of success is higher and leadership will have a stake in the outcome.
Share a Vision
As an extension of upper management buy-in, there needs to be clear and aspirational communication about the value of process improvement, both for the organization, but also for employees and customers.
The most effective way to do this is to share a vision. Paint a picture of what the outcomes of the process change can be. How will work and the output of the company be improved? How will all the employees be positively impacted? How will customers benefit?
The vision becomes the North Star that serves to not only get the team excited but also to understand what it is they are working toward. It also validates the buy-in from leadership.
Orient Work Towards Processes and Outcomes
Many traditional workplaces are structured around siloed departments with their attendant functions. Often these departments operate independently with unique methodologies and cultures. This can create situations where departments develop habitual ways of doing things that can resist process improvement. Each department may find ways to streamline work for themselves but this doesn't always account for where the task fits in the process as a whole.
With process improvement models like Lean Six Sigma, work orientation shifts to a focus on processes and outcomes. Teams are now assigned well-defined projects that directly affect the organization's bottom line. They are no longer simply completing a task or function, they are playing an integral role in a process with a clearly defined outcome. Ideally, job titles and department names should change to reflect this re-orientation, as well as the stated goals and expectations of the teams and team members.
What Gets Measured, Gets Managed
Measurement and analysis are important elements of process improvement, so it should go without saying that creating a culture of process improvement is also going to require a culture that seeks to quantify as many elements of their work as possible.
There are many aspects of work that will resist measurement, but finding creative and accurate ways to measure around even the fuzziest of business elements can be important in building out the process improvement culture in general.
Provide Training
Even if your team is already familiar with the concepts of Lean Six Sigma or other process improvement methodologies, there is always value in offering continued education. This can even include extending process improvement training to employees that may not always be doing the direct work of process improvement but could still benefit from understanding the concepts.
Managers, directors and other levels of leadership can benefit from guidance on how to build an effective problem-solving culture. The Division of Extended Studies offers a Lean Six Sigma Leadership course and other custom corporate trainings that can help them identify the most impactful areas for improvement from their point of view. This training serves to not only ensure your staff is always current on their skill set, but also creates an important pipeline of talent that can continue to step into important roles as your company grows.
UC San Diego Division of Extended Studies offers several other Lean Six Sigma courses and certifications to help your team grow their knowledge of process improvement:
- Lean Six Sigma Yellow Belt: Earning a Lean Six Sigma Yellow Belt is an ideal starting point for those ready to tackle inefficient processes and embrace streamlined efficient ways of working in any business or industry.
- Lean Six Sigmas Green and Black Belt Certificate: This program, which can alternatively be broken into two parts (Green Belt and Black Belt), is beneficial for participants who have process improvement responsibilities and wish to advance their careers, as well as those individuals who are new to the toolset.
We’ve only covered the tip of the iceberg when it comes to creating a thriving culture of process improvement within your company. Hopefully, you can already see how such a shift could be of value to your organization and have some ideas for what you can do to institute it. With diligence and commitment, you can assuredly experience more significant growth in the long term, too.
Discover firsthand how UC San Diego has made Process Improvement an integral part of our culture. Join us March 28 & 29 for Process Palooza, our high-energy collaborative experience showcasing and celebrating the power of continuous improvement through competitions, hands-on learning and interactive exhibits in our community pavilion.
By participating in Process Palooza, you’ll become a part of a community of change-makers, leaders, and decision-makers from various industries including higher education, manufacturing, information technology, healthcare and professional organizations from San Diego, the U.S. and across the globe.
To learn more about Project Management and Lean Six Sigma programs at UC San Diego Division of Extended Studies, visit https://go.ucsd.edu/3INLad8.