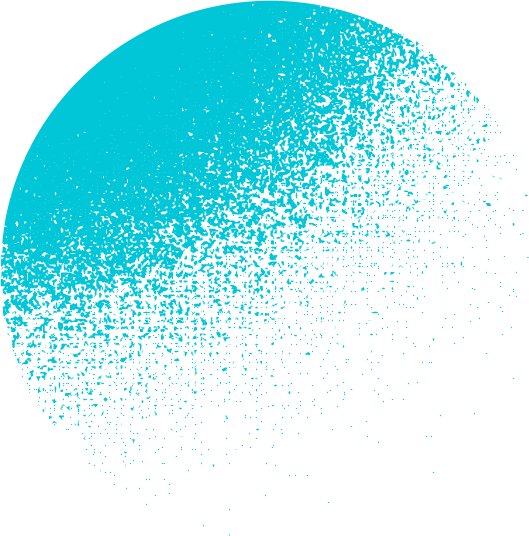
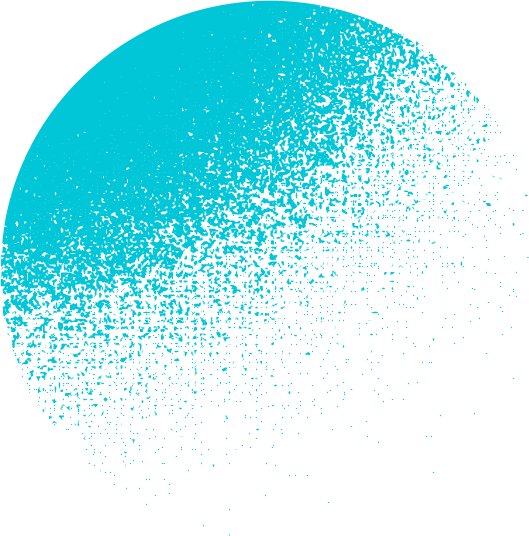
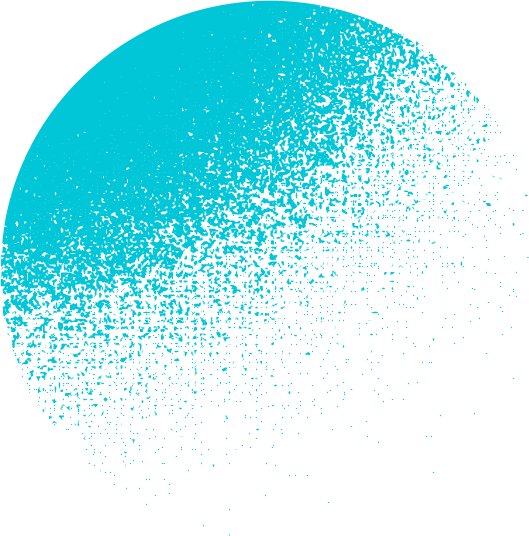
2 February 2012
Will the 'real' Lean Enterprise please stand up?
By Jerry Wright
It’s been nearly 3 decades since the continuous improvement management system known as “lean” really began in the corporate world. Lean essentially means without waste and seeks to create value for the customer. Anything that does not add value in the eyes of the customer is waste and should be eliminated or at least reduced. Initially, lean was heavily focused in the automotive industry but has since moved to all industry, the service sector and now even government and health care. This would sound great, but there’s a dark cloud in front of the silver lining.
Many supposed lean enterprises have done all of the right things: they have hired lean consultants to provide training, they have conducted Kaizen (Japanese for Continuous Improvement) events, completed workplace organization (known as 5S) and even created standard work. Yes, these are some of the key foundations of a lean enterprise. However, as most seasoned lean veterans will tell you, this can be nothing more than window dressing. One can visit numerous facilities and see what looks like a very clean, well-organized and seemingly disciplined business that calls itself lean. Upon further examination, you may find a sluggish set of processes that are still laden with busy work that really does not create any value for the customer.
So, how can you cut through the façade and understand if the business really is becoming lean? Well, the “real” lean enterprises will tell you that while they have made good progress, they still have much to improve. Lean is a “journey” and not a destination. That being said, dig a little deeper on some key measures. Are quality complaints trending downward? Are inventory turns improving? Are customer satisfaction measures collected, posted and are their issues being addressed? Is production based on actual customer demand (meaning do we only build to order or replace inventory only when sold)? Is the business actually profitable? If the measures are accurate, these can tell you a lot.
Last, let your eyes tell you the real story in the production or value-creating process. Is there only one piece of work or order in process per person? Or do you see “batches” of work being pushed from one person or area to another? The latter is undesirable, as you may guess. Do employees follow very specific work routines and almost appear as though they are choreographed or is it a little chaotic? Each day our work will have variation but we should have more of a theater production rather than a hockey game in our important business processes per quality guru and author Phillip Crosby. Both may be fun to watch, he states, but one has a rather predictable outcome and the other does not.
Would you like to be able to spot “fake” flow and understand what a lean enterprise really is? Attend an upcoming free information session to learn more about UC San Diego Extension's Lean Enterprise program.
Jerrald Wright, MBA, P.E., is the Lead Instructor for UC San Diego Extension’s Lean Enterprise Certificate Program. Jerry is currently the President of LEANwRIGHT, Inc., a management consulting firm specializing in Lean Transformation. Prior to leading his own firm, he was the Senior Vice President of DJO Global, Inc., a global medical device manufacturer with $1.1 Billion Sales. At DJO, he was one of the key change leaders that helped to introduce lean thinking and transformed the company from a traditional batch and queue manufacturer to a world-class, lean enterprise. He holds a B.S. in Mechanical Engineering from Arizona State University, and an MBA from the University of Phoenix. Jerry is a licensed Professional Engineer in the State of California and the holder of one U.S. patent. He is also the Chair of the Southern California Lean Network, an association of more than 90 companies that meet bimonthly to share best practices in lean, excellence and continuous improvement.