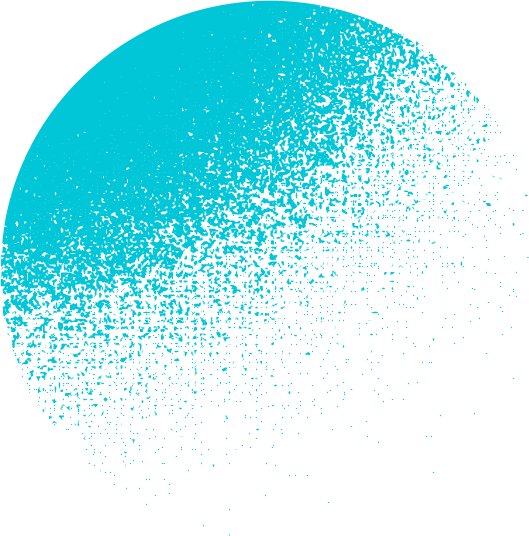
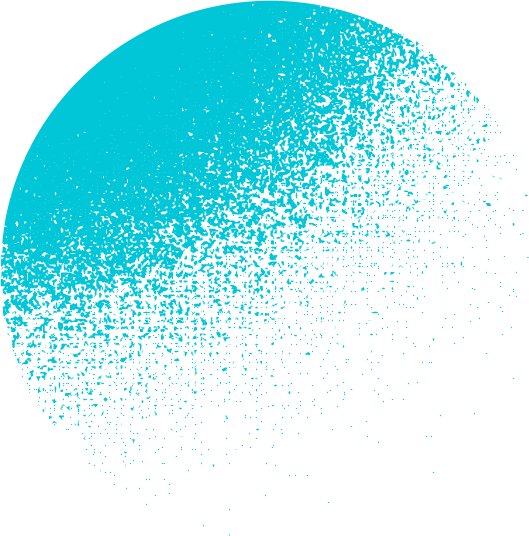
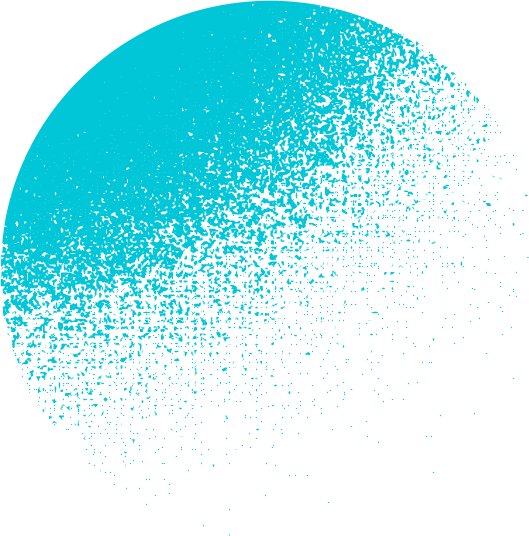
13 April 2022
How the Principles of Lean Six Sigma Can Help You
Regardless of what industry you work in, there has likely come a time when you felt frustrated and sure there was a better way of doing things but were unsure how to speak to the root issue, let alone consider possible solutions.
At its most basic, Lean Six Sigma is a strategic approach to implementing continuous improvement that can be applied to any industry.
It combines two powerful strategies to help you effectively identify problems and inefficiencies so you can figure out how to streamline your process to eliminate waste and ensure quality output. The result is higher customer/end-user satisfaction, increased morale among those actively engaged in the production or service process, and increased profitability for the business itself.
Professionals can work towards different levels of certification in Lean Six Sigma, which are divided into belt colors, with the first level being white and the highest level being black (think martial arts). And though Lean Six Sigma was initially developed for the manufacturing industry, the principles apply to everything from hospitality to healthcare. It can even be used to streamline the processes in your daily life. That's because it's a process of strategic problem-solving.
To better understand this methodology, it's best to start by examining the two underlying practices of Lean and Six Sigma.
What is Lean?
Lean was a process developed in the 1930s by Kiichiro Toyoda, the owner of Toyota, and his industrial engineer Taiichi Ohno to improve upon Henry Ford's automotive production model. They developed the Toyota Production System after identifying the seven most common wastes in manufacturing and creating a system to minimize them.
An eighth waste was added in the 1990s. The process now focuses on eliminating DOWNTIME, which stands for Defects, Overproduction, Waiting, Not utilizing talent, Transportation, Inventory excess, Motion waste and Excess processing.
What is Six Sigma?
Six Sigma (6σ) is a set of techniques and tools for process improvement. It comes from the statistical modeling of a manufacturing process expected to be free of defects 99.99966% of the time. Six Sigma aims to improve process output quality by identifying and removing the causes of defects or errors and minimizing variability in manufacturing and business processes.
The method was developed in 1986 by an American engineer, Bill Smith, working at Motorola, where the company made a "Six Sigma" goal for all its manufacturing. General Electric followed suit, and in 1995 CEO Jack Welch made it an essential aspect of his business strategy. He said: "We are going to shift the paradigm from fixing products to fixing and developing processes, so they produce nothing but perfection or close to it."
Near perfection is a lofty goal, but the strategy paid off, and in 1998, the company announced that it had saved $350 million in production costs by using the Six Sigma process. Within two years, roughly two-thirds of all Fortune 500 companies used the process to reduce costs and improve quality.
Lean Six Sigma is a Powerful and Adaptable Combination
A focus on process change is at the heart of Lean and Six Sigma. And while Lean is essentially creating a system that needs less of everything (time, energy, inputs, etc.) to create a set output, Six Sigma provides a powerful problem-solving element to the method.
There are five phases used in Lean Six Sigma to identify the root cause of inefficiencies, improve the process and solve the problem.
A simple example of how one might use Lean Six Sigma to solve a non-manufacturing issue is to look at a person who is always late to work. Let's call that person Dave. After learning about Lean Six Sigma, Dave has decided to try to apply the principles to his own life.
The first thing Dave has to do is define the problem. That's easy! He's always late, and that's a problem because he gets fired if he keeps it up.
The next phase is to measure or quantify the problem. Late is vague. How late is he exactly, and how often? He looks back at his timecards for the last month and discovers a pattern. He is consistently five to ten minutes late on Tuesday, Wednesday, and Thursday, but he is on time on Mondays and Fridays. That information will help in the next phase: identifying the root issue.
In the Analysis phase, Dave spends the next week noting what is different about his morning routine and commute on the days he is typically late. He discovers that his wife leaves earlier for work than he does Tuesday to Thursday, which means he has to take the dog out before he heads to the office, something she usually handles.
In the Improve phase, Dave identifies several options for solving the root issue. He could get up earlier those days to give himself extra time to take care of his pet, but that would do nothing to help resolve the underlying wastes of motion (taking the dog outside) and waiting (once outside). So, Dave decides to try a different solution to eliminate the inefficiency in his morning routine altogether. He installs a dog door so his pup can let himself out each morning. The following week he verifies improvement by analyzing the effect of his solution. He finds that he is on time every day, so installing the dog door has effectively improved his process of getting to work on time.
In the final control phase, Dave reviews his timecards at the end of the month to make sure his process improvement has completely solved the problem. Dave finds that his tardiness has improved significantly, but not completely. He is now on time every day except Thursday, when, after the first week of success, he has been five minutes late every week since. To continue improving his process, Dave will go back to the analysis phase to look for other wastes or inefficiencies that could be contributing to this issue, so he can then improve upon them.
Lean Six Sigma has the power to do far more than help you get to work on time; it is a strategic approach to continually improving the way your business functions that can yield powerful results for everyone involved. Every company can benefit from Lean Six Sigma training for managers and frontline employees. The payoff is immense, from improving customer satisfaction to empowering employees to be active problem solvers. It's a strategy that not only improves profits but aims to future-proof companies through a culture shift towards continuous improvement.
Did you find this article interesting or helpful? Let us know in the comments!