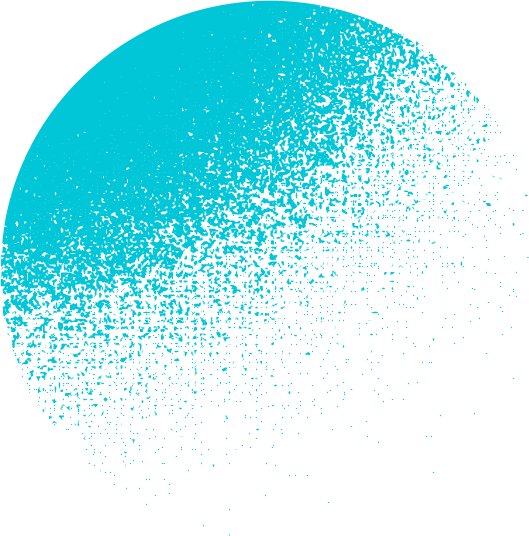
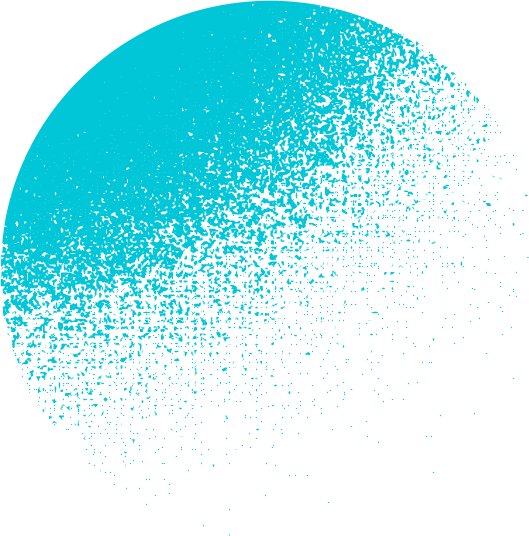
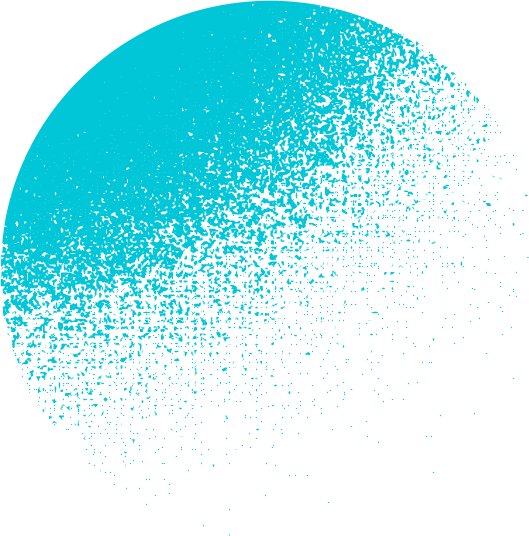
1 May 2015
Lean Six Sigma Black Belt: A constant process of improvement
For Maya Gowri, implementing operational excellence is pivotal to her official role at Inova Diagnostics, a San Diego-based manufacturer of in vitro diagnostic systems used in clinical immunology labs and hospitals around the world.
Inova hired Gowri after taking her on as an intern while she completed UC San Diego Extension’s Lean Six Sigma Black Belt (LSSBB) and Lean Enterprise certificate programs. The internship provided an opportunity for Maya to complete her required hands-on course project, which showcased both her potential and her achievement in Extension’s process improvement programs.
Lean Six Sigma is a highly-regarded toolset that combines Lean Enterprise and Six Sigma methodologies. Its roots are in manufacturing, and it has since evolved as an effective tool in a wide range of industries, from finance and hospitality to telecommunications and transportation. In Lean Six Sigma, the Black Belt is the highest level of achievement—it is outranked by only the Master Black Belt, which recognizes an expert who serves primarily in the role of coach.
“I had never been in manufacturing or production before, so I had no idea what to expect when I started my courses,” said Gowri, who formerly worked in marketing, business development, and sales. “It was all new to me, but the knowledge I gained from the certificate programs helped me catch on quickly.”
“The certificate program was well-structured and well-paced, which gave us enough time to fully grasp the concepts,” said Gowri, who previously worked at Tri-City Medical Center in Oceanside as a senior improvement analyst. “Plus, the Lean Enterprise course included three on-site visits to manufacturing plants, which helped us see concepts being implemented.”
In her studies, Gowri discovered that Lean Six Sigma places strong emphasis on practical process-driven knowledge and on the value of person-to-person relations.
“People are any company’s most valuable asset,” she said. “As part of leadership skills, we learned to fully embrace the concept of humility. Even though you’re the leader, you need to step back and give full credit to your team.”
While she’s not yet prepared to describe herself as an expert—“I’m in a constant process of improvement”—Gowri now considers herself to be knowledgeable, confident, and well-disciplined in the complex production process she oversees.
As an Operational Excellence Leader, Maya plays a part in the mission of Inova Diagnostics, where advanced medical products help in the diagnosis of serious ailments such as celiac disease, liver disease, rheumatoid arthritis, autoimmune thyroid disease, and vasculitis, among others. In 2014, for example, the company introduced a new agent that aids in the diagnosis of inflammatory bowel disease (IBD).
Maya’s completion of her certificates did not close the door on her relationship with UC San Diego Extension. Maya facilitated the creation of three project sponsorships for Inova Diagnostics through the Lean Six Sigma Black Belt program.
“Maya truly implemented Lean Six Sigma methodologies at Inova by making it an organizational priority to bring in Lean Six Sigma students,” says Angela Cook, Program Manager for Process Improvement at Extension. “Her influence helped give opportunities to students, which in turn gave Inova a connection to top local talent.”
Gowri, who holds an MBA from UC Irvine and a Ph.D. from the University of Kentucky, moved to the United States from India in 1993. Her global background helped give her the perspective to meld various managerial styles within Inova’s diverse workforce.
“The Indian culture is family-oriented and team-oriented, whereas the American culture is more individual-oriented,” she said. “I try to focus on the uniqueness of each person, to see them all as people instead of simply employees.”